Um Blechbiegeteile ordentlich biegen zu können müssen gewisse Parameter eingehalten werden. Diese varieren zwar je nach Maschinentyp und Fertigungsmöglichkeiten etwas. Aber nach aktuellem Stand der Technik sind folgende Parameter ohne Probleme nutzbar. Wir nutzen diese schon einige Jahre ohne bisherige Probleme.
Es ist wichtig zu beachten, dass für konstruktionsbedingten Verzug der Biegeteile der Hersteller in der Regel keine Verantwortung übernimmt. Daher ist es von entscheidender Bedeutung, bei der Konstruktion und Planung von Blechteilen diese Aspekte sorgfältig zu berücksichtigen und gegebenenfalls mit dem Hersteller zu kommunizieren.
Insgesamt ist die Vermeidung von Verzug beim Biegen von Blechteilen ein wichtiger Schritt, um hochwertige und präzise gefertigte Produkte zu erhalten.
1. Mindestschenkellänge
Die hier angegebenen Mindestschenkellängen dürfen nicht unterschritten werden.
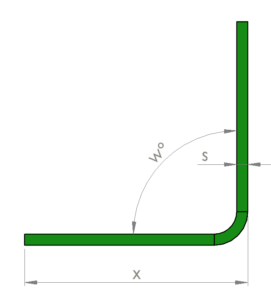
Mindestschenkellänge für Stahl
Blechdicke (s) | x für Winkel ≥ 90° (w) | x für Winkel < 90° (w) |
---|---|---|
0,5 mm | 5mm | 8mm |
0,8 mm | 5 mm | 10 mm |
1 mm | 5,5 mm | 10 mm |
1,5 mm | 9 mm | 10,5 mm |
2 mm | 9,5 mm | 13 mm |
2,5 mm | 12 mm | 15,5 mm |
3 mm | 14 mm | 22 mm |
4 mm | 18,5 mm | 23 mm |
5 mm | 24 mm | 30 mm |
6 mm | 30 mm | 38 mm |
8 mm | 38 mm | 45 mm |
10 mm | 45 mm | 59 mm |
12 mm | 59 mm | 88 mm |
15 mm | 88 mm |
Mindestschenkellänge für Edelstahl und Aluminium
Blechdicke (s) | x für Winkel ≥ 90° (w) | x für Winkel < 90° (w) |
---|---|---|
0,5 mm | 5mm | 8mm |
0,8 mm | 5 mm | 10 mm |
1 mm | 5,5 mm | 10 mm |
1,5 mm | 9 mm | 10,5 mm |
2 mm | 9,5 mm | 13 mm |
2,5 mm | 12 mm | 15,5 mm |
3 mm | 15,5 mm | 22 mm |
4 mm | 22,5 mm | 27 mm |
5 mm | 30 mm | 38 mm |
6 mm | 38 mm | 43 mm |
8 mm | 43 mm | 57 mm |
10 mm | 57 mm | 72 mm |
12 mm | 72 mm | |
15 mm | 104 mm |
2. Mindestabstand Innenkontur zur Biegung
Beim Biegen von Blechteilen ist es entscheidend, ausreichend Abstand zwischen Bohrungen, Aussparungen oder Konturen und den Biegekanten einzuhalten. Andernfalls besteht das Risiko, dass sich diese Elemente während des Biegevorgangs verziehen. Der Mindestabstand zur Biegung entspricht der Mindestschenkellänge des Materials (siehe Tabellen oben). Das x-Maß gibt den Abstand bis zur Kontur an.
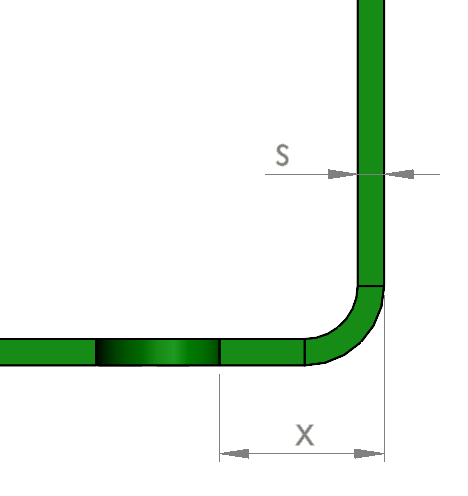
In einigen Fällen ist es konstruktionsbedingt unvermeidlich, dass Bohrungen oder Konturen nahe an der Biegekante platziert werden müssen. In solchen Situationen können Entlastungsschnitte eine Lösung sein. Durch das Einbringen von Entlastungsschnitten in strategische Bereiche können Spannungen reduziert und das Risiko von Verzug minimiert werden.
3. Entlastungsschnitte
Wenn der Mindestlochabstand aus konstruktiven Gründen nicht eingehalten werden kann, bieten Entlastungsschnitte eine effektive Lösung, um Verzug bei Bohrungen oder Aussparungen nahe der Biegezone zu verhindern. Die Gestaltung dieser Entlastungsschnitte erfordert jedoch besondere Aufmerksamkeit. Hier sind einige wichtige Punkte zu beachten:
Stabilität des Bauteils: Es ist unerlässlich, dass trotz der Entlastungsschnitte noch ausreichend Material in der Biegezone vorhanden ist, um die Stabilität des Bauteils sicherzustellen. Ein zu großzügiges Freischneiden könnte die Struktur des Bauteils beeinträchtigen und seine Festigkeit reduzieren.
Vermeidung von scharfkantigen Aussparungen: Scharfkantige Aussparungen wie Rechtecke können zu Schwachstellen führen, die das Risiko von Rissen erhöhen. Dies geschieht insbesondere an den Ecken, wo das Material am stärksten belastet wird. Um dieses Risiko zu minimieren, sollten die Entlastungsschnitte so gestaltet werden, dass scharfe Kanten vermieden werden.
Die ideale Form für Entlastungsschnitte: Um eine optimale Entlastung der Biegezone zu gewährleisten, ist die Verwendung einer rechteckigen Aussparung mit abgerundeten Ecken empfehlenswert. Diese Form reduziert nicht nur das Risiko von Rissen, sondern erleichtert auch den Biegeprozess und sorgt für eine gleichmäßige Verteilung der Spannungen.
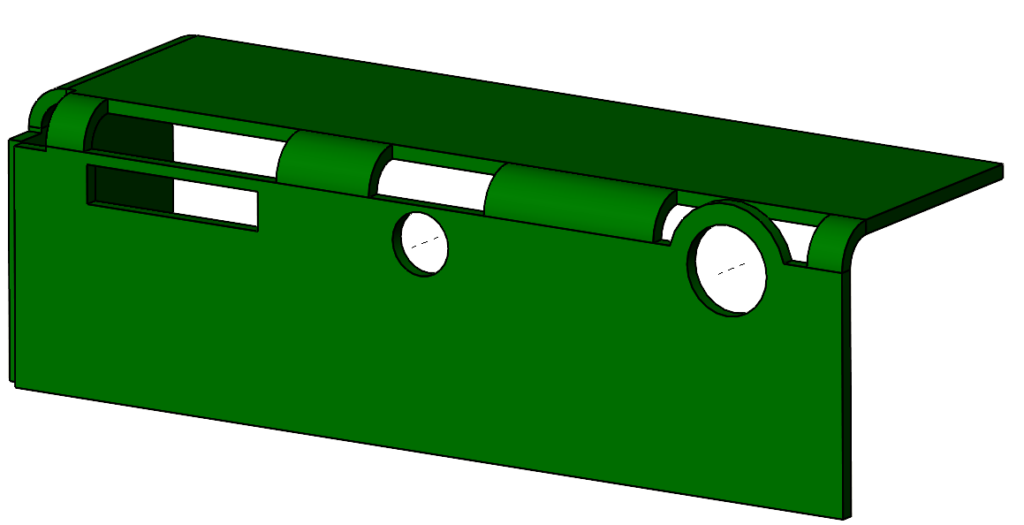
Durch die Berücksichtigung dieser Punkte bei der Konstruktion von Entlastungsschnitten können Sie sicherstellen, dass Ihre Blechteile trotz der Nähe zur Biegezone präzise gefertigt werden und Verzug vermieden wird.
4. Mindestabstand Außenkontur zur Biegung
Wenn ein Bauteil spitze Biegungen oder andere spezifische Außenformen in der Nähe von Biegekanten aufweist, gelten dieselben Bestimmungen wie für die geforderte Mindestlänge des Biegeschenkels. Ab einer gewissen Grenze unterschreitet die Länge des Biegeschenkels die Mindestanforderung aufgrund der Kontur, was dazu führt, dass das Material nicht länger vollständig auf dem unteren Werkzeug, der Matrize, aufliegt. Dies kann zur Folge haben, dass sich der betreffende Bereich während des Biegeprozesses verformt oder nicht gänzlich umgebogen wird, was eine unvollständige Biegung zur Folge hat. Beispielsweise können Bereiche des Biegeschenkels nicht vollständig umgebogen sein.
Zur Vermeidung dieser Problematik stehen drei Optionen zur Verfügung:
- Die Entfernung der Biegung im betroffenen Bereich,
- Die Anpassung der Biegung im betroffenen Bereich, um die Mindestschenkellänge zu erreichen, oder
- Das Freischneiden der Biegung, um zu verhindern, dass der betroffene Bereich mitgebogen werden muss.
5. Mindesthöhe Z-Biegung
Bei zwei aufeinanderfolgenden Biegungen (Z-Biegung) entstehen werkzeugbedingt folgende Mindestmaße:
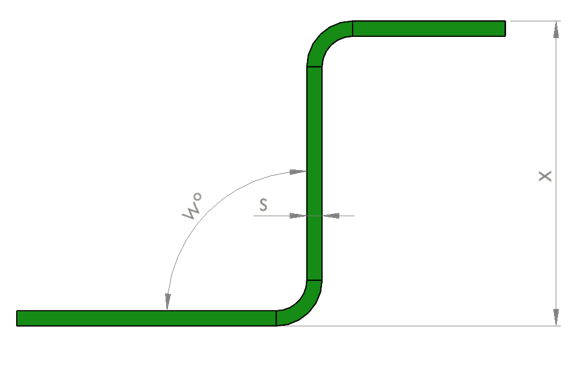
Stufenhöhe Z-Biegung Stahl
Blechdicke (s) | x für Winkel ≥ 90° (w) | x für Winkel < 90° (w) |
---|---|---|
1 mm | 11,5 mm | 19 mm |
1,5 mm | 13,5 mm | 20 mm |
2 mm | 18 mm | 26,5 mm |
2,5 mm | 24 mm | 32,5 mm |
3 mm | 26 mm | 36 mm |
4 mm | 36 mm | 53 mm |
5 mm | 43,5 mm | 53 mm |
6 mm | 53,5 mm | 63,5 mm |
8 mm | 65,5 mm | 78 mm |
10 mm | 92 mm | |
12 mm | 109 mm | |
15 mm | 181 mm |
Stufenhöhe Z-Biegung für Edelstahl und Aluminium
Blechdicke (s) | x für Winkel ≥ 90° (w) | x für Winkel < 90° (w) |
---|---|---|
1 mm | 11,5 mm | 19 mm |
1,5 mm | 13,5 mm | 20 mm |
2 mm | 18 mm | 26,5 mm |
2,5 mm | 24 mm | 32,5 mm |
3 mm | 26 mm | 36 mm |
4 mm | 36 mm | 53 mm |
5 mm | 43,5 mm | 53 mm |
6 mm | 53,5 mm | 63,5 mm |
8 mm | 65,5 mm | 78 mm |
10 mm | 92 mm | |
12 mm | 109 mm | |
15 mm | 181 mm |
6. Maximale Schenkellänge
Zusammenstoß mit dem Werkzeug bei der Fertigung von U-Profilen
Wenn die Schenkel des Biegeteils zu ausgedehnt sind oder das Design des U-Profils zu eng gestaltet ist, besteht das Risiko eines Zusammenstoßes mit dem oberen Werkzeug (dem Stempel) oder dem darüber befindlichen Pressbalken. Die machbaren Dimensionen für U-Profile lassen sich anhand der untenstehenden Diagramme erkennen.
Sobald die Materialdicke 6 mm überschreitet, ist die Nutzung eines gekröpften Stempels aufgrund der spezifischen Geometrie und der Größe des Bauteils oft nicht mehr möglich, stattdessen muss ein gerader Stempel eingesetzt werden.
Werkzeuge mit Hörnern
Werkzeuge, die mit seitlichen Ausläufern, bekannt als Hörner, ausgestattet sind, ermöglichen die Herstellung von verborgenen Biegekanten in geschlossenen Rahmendesigns. Für solche verdeckten Biegungen darf der Bereich maximal 32 mm umfassen und muss in seiner Höhe ausreichend Raum für das Einsetzen des Horns bieten.
7. Biegeradius
- Die angegebenen Radien können in Abhängigkeit vom eingesetzten Werkzeug beträchtlich variieren.
- Vor allem die Wahl der Biegematrize bestimmt den Innenradius des Biegeteils, während die Auswahl des Biegestempels nur einen geringfügigen Einfluss darauf hat.
- Die tatsächlichen Biegeinnenradien können aufgrund unterschiedlicher Materialchargen, dem Zustand des Werkzeugs sowie der spezifischen Bauteilgeometrie variieren.
- Vorgegebene Radien im Konstruktionsprozess werden bei der Herstellung nicht berücksichtigt und standardmäßig auf Werte innerhalb des angegebenen Bereichs angepasst, sofern keine spezifische Anfrage Ihrerseits vorliegt.
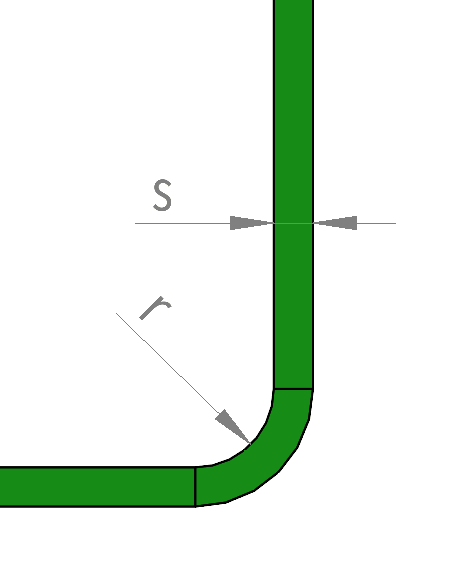
Biegeradien bei 90° Biegungen
Stahl
Blechdicke (t) | Radius OW | Gesenkweite UW | Biegeinnenradius |
---|---|---|---|
0,5 | 0,5-1 | 4-8 | ca. 0,5-1,7 |
0,8 | 0,5-1 | 4-12 | ca. 0,8-2,5 |
1 | 1 | 6-12 | ca. 1,0-2,5 |
1,5 | 1 | 6-16 | ca. 1,5-3,4 |
2 | 1-2 | 10-20 | ca. 2,0-4,2 |
2,5 | 1-2,5 | 12-24 | ca. 2,5-5,0 |
3 | 1-3 | 16-30 | ca. 3,0-6,3 |
4 | 1-4 | 20-40 | ca. 4,0-8,0 |
5 | 1-5 | 30-50 | ca. 5,0-10,1 |
6 | 1-6 | 30-60 | ca. 6,0-11,8 |
8 | 4-8 | 50-90 | ca. 10,2-18,1 |
10 | 4-10 | 70-120 | ca. 14,0-24,2 |
12 | 5-10 | 80-120 | ca. 15,8-24,4 |
15 | 6-10 | 90-120 | ca. 17,9-24,1 |
Edelstahl
Blechdicke (t) | Radius OW | Gesenkweite UW | Biegeinnenradius |
---|---|---|---|
0,5 | 0,5-1 | 4-8 | ca. 0,5-1,8 |
0,8 | 0,5-1 | 4-12 | ca. 0,8-2,6 |
1 | 1 | 6-12 | ca. 1,0-2,7 |
1,5 | 1 | 6-16 | ca. 1,5-3,7 |
2 | 1-2 | 10-20 | ca. 2,0-4,6 |
2,5 | 1-2,5 | 12-24 | ca. 2,5-5,7 |
3 | 1-3 | 16-30 | ca. 3,0-7,0 |
4 | 1-4 | 20-40 | ca. 4,0-9,0 |
5 | 1-5 | 30-50 | ca. 7,3-11,2 |
6 | 1-6 | 30-60 | ca. 7,2-13,6 |
8 | 4-8 | 50-90 | ca. 12,2-19,9 |
10 | 4-10 | 70-120 | ca. 16,1-26,6 |
12 | 4-10 | 80-120 | ca. 18,5-27,3 |
15 | 4-10 | 90-120 | ca. 21,0-27,8 |
Aluminium
Blechdicke (t) | Radius OW | Gesenkweite UW | Biegeinnenradius |
---|---|---|---|
0,5 | 0,5-1 | 4-8 | ca. 1,3-2,1 |
0,8 | 0,5-1 | 4-12 | ca. 1,2-3,0 |
1 | 1 | 6-12 | ca. 1,6-3,0 |
1,5 | 1 | 6-16 | ca. 1,6-4,0 |
2 | 1-2 | 10-20 | ca. 2,6-5,0 |
2,5 | 1-2,5 | 12-24 | ca. 2,8-5,9 |
3 | 1-3 | 16-30 | ca. 3,8-7,5 |
4 | 1-4 | 20-40 | ca. 4,6-19,6 |
5 | 1-5 | 30-50 | ca. 6,9-12,0 |
6 | 1-6 | 30-60 | ca. 6,9-14,1 |
8 | 4-8 | 50-90 | ca. 12,0-21,6 |
10 | 4-10 | 70-120 | ca. 16,1-29,6 |
12 | 5-10 | 80-120 | ca. 21,9-29,1 |
15 | 6-10 | 90-120 | ca. 20,4-28,5 |
Biegewinkel unter 90°
Bitte beachten Sie folgende Richtlinien für das Biegen von Blechen mit Biegewinkeln unter 90°:
- Bei Blechdicken bis zu 5 mm ist die Nutzung von Biegematrizen zu empfehlen, deren Gesenköffnung maximal 30° beträgt.
- Für Blechdicken von 6 mm und darüber hinaus ist der Einsatz von Biegematrizen ratsam, die eine Gesenköffnung von 60-80° aufweisen.
- Das Risiko für die Entstehung von Rissen steigt bei Blechdicken ab 3 mm signifikant an, besonders bei der Anwendung kleinerer Biegewinkel.
- Schmale Biegeflansche können die Gefahr der Rissbildung verstärken.
- Vor allem bei Aluminiumblechen kann diese Problematik bereits bei geringeren Materialdicken auftreten.
Biegewinkel < 90° | Blechdicke Stahl | Blechdicke Edelstahl | Blechdicke Aluminium |
---|---|---|---|
< 30° | – | – | – |
30-35° | bis 2,0 mm | bis 2,0 mm | – |
35-40° | bis 4,0 mm | bis 4,0 mm | bis 2,0 mm |
40-45° | bis 6,0 mm | bis 6,0 mm | bis 2,5 mm |
45-60° | bis 8,0 mm | bis 8,0 mm | bis 2,5 mm |
60-80° | nicht begrenzt | nicht begrenzt | bis 5,0 mm |
Falzbiegungen (180°)
Für die Ausführung von 180°-Falzbiegungen gelten folgende Richtlinien:
- Die Materialstärke darf bei solchen Biegungen höchstens 2 mm betragen.
- Beim Design des Falzes sollte ein Abstand von 0,2 mm eingeplant werden. Allerdings ist zu berücksichtigen, dass der Falz im Verlauf der Produktion geschlossen wird.
Je nach Blechdicke müssen andere Falzlängen mindestens eingehalten werden.
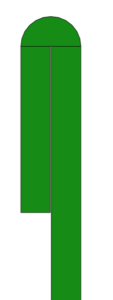
Blechdicke (s) | x für Winkel < 90° (w) |
---|---|
0,5 mm | 10 mm |
0,8 mm | 10 mm |
1 mm | 10 mm |
1,5 mm | 10,5 mm |
2 mm | 13 mm |
8. kleinstmögliche Lochgröße beim Laserschneiden
Beim Laserschneiden müssen können technologie bedingt gewisse Lochgrößen nicht unterschritten werden. Diese sind abhängig von der Blechdicke und vom Werkstoff.
Stahl
Blechdicke (s) | kleinstmögliche Lochgröße |
---|---|
1,0 mm | Ø0,5 mm |
1,5 mm | Ø0,8 mm |
2,0 mm | Ø1,0 mm |
3,0 mm | Ø2,0 mm |
4,0 mm | Ø2,5 mm |
5,0 mm | Ø3,2 mm |
6,0 mm | Ø3,2 mm |
8,0 mm | Ø4,5 mm |
10,0 mm | Ø6,0 mm |
12,0 mm | Ø7,0 mm |
15,0 mm | Ø9,0 mm |
20,0 mm | Ø14,0 mm |
25,0 mm | Ø22,0 mm |
Edelstahl
Blechdicke (s) | kleinstmögliche Lochgröße |
---|---|
1,0 mm | Ø0,8 mm |
1,5 mm | Ø1,0 mm |
2,0 mm | Ø1,0 mm |
3,0 mm | Ø1,5 mm |
4,0 mm | Ø2,0 mm |
5,0 mm | Ø3,0 mm |
6,0 mm | Ø3,2 mm |
8,0 mm | Ø4,0 mm |
10,0 mm | Ø5,0 mm |
12,0 mm | Ø9,0 mm |
15,0 mm | Ø10,0 mm |
20,0 mm | Ø19,0 mm |
25,0 mm | - |
Aluminium
Blechdicke (s) | kleinstmögliche Lochgröße |
---|---|
1,0 mm | Ø1,0 mm |
1,5 mm | Ø1,5 mm |
2,0 mm | Ø2,0 mm |
3,0 mm | Ø2,5 mm |
4,0 mm | Ø3,0 mm |
5,0 mm | Ø3,5 mm |
6,0 mm | Ø4,0 mm |
8,0 mm | Ø7,0 mm |
10,0 mm | Ø8,0 mm |
12,0 mm | Ø10,0 mm |
15,0 mm | - |
20,0 mm | - |
25,0 mm | - |
9. Biegefreistich
Aufgrund der Tatsache, dass Laserschnitte eine bestimmte Mindestbreite aufweisen können Biegefreistiche nicht beliebig ausgeführt werden und müssen sich an Mindestbreiten für Laserschnitte halten.
Ohne einen geeigneten Abstand zwischen den Biegebereichen könnte das Material entlang des Schnittes weiterhin reißen. Ein geeigneter Abstand verhindert Kerbwirkungen und ermöglicht ein korrektes Biegen des Teils. Eine Schlitzbreite von mindestens 1 mm mit abgerundeten Ecken wird empfohlen.
Entlastungsschnitte neben Biegungen müssen eine Mindestbreite und -tiefe aufweisen, die der Materialdicke entspricht. Es ist essenziell, genügend Freiraum um die Biegungen zu lassen, um eine genaue Bearbeitung und die Stabilität des Bauteils zu sichern. Entlastungsschnitte neben Biegungen Entlastungsschnitte an Ecken

Die Entlastungsschnitte an den Ecken sollten in jeder Richtung mindestens 1 mm über die Biegung hinausgehen. Diese zusätzliche Länge schafft genug Platz für die Biegung und kann je nach Materialdicke in der Produktion angepasst werden.
Der Abstand zwischen zwei benachbarten Laschen muss mindestens 0,2 mm betragen, um eine akkurate Bearbeitung zu ermöglichen. Es ist wichtig, genügend Zwischenraum für eine präzise und effiziente Bearbeitung zu lassen.
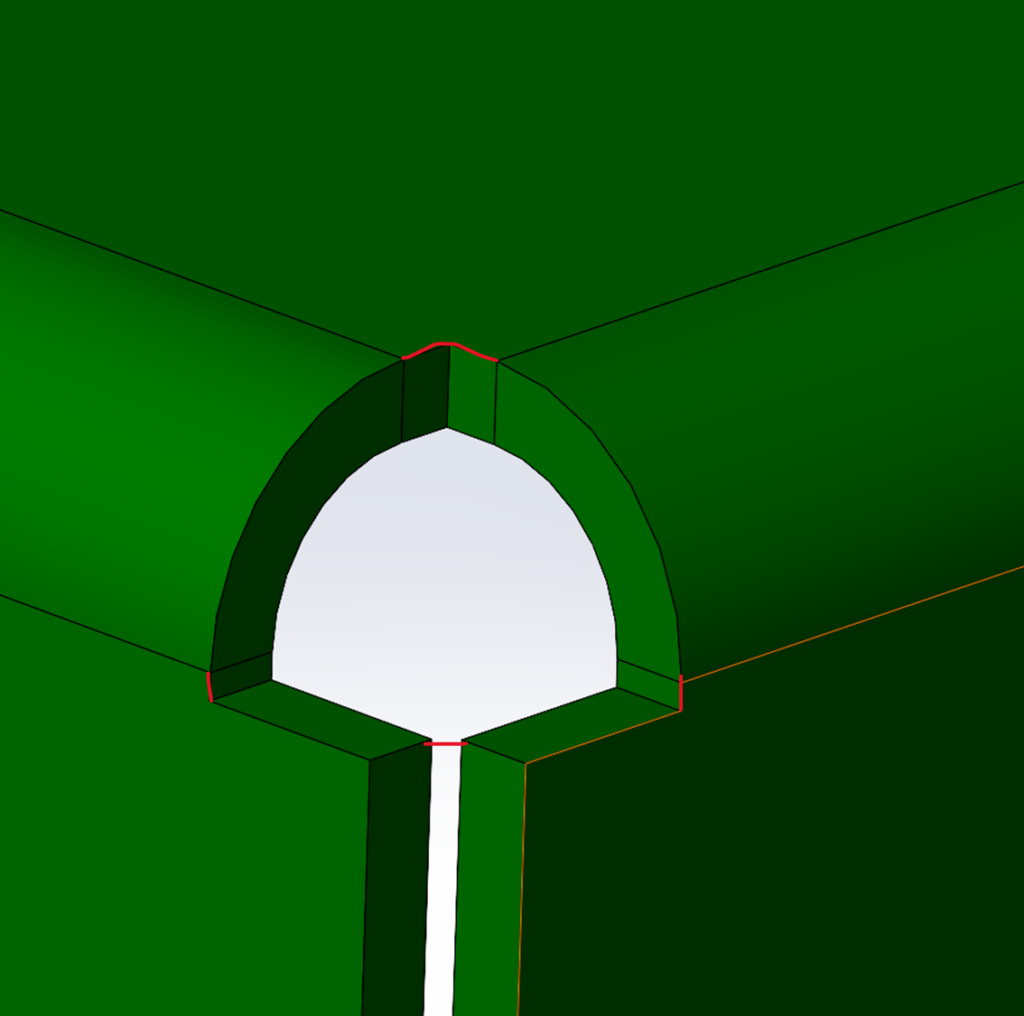
10. Mindestmaße für Laserschnitt
Trotz der hohen Präzision von Laserschnitten gibt es Beschränkungen, die bei intensiver Energiezufuhr auf eine kleine Fläche die erwartete Qualität beeinträchtigen können. Daher ist es wichtig, die folgenden Mindestabmessungen bei der Gestaltung von Metallteilen zu berücksichtigen:
- Mindestdurchmesser für Löcher = 0,7 x Dicke des Materials oder siehe Kapitel 8.
- Mindestbreite für Stege und Schlitze = 0,7 x Dicke des Materials (beispielsweise für Belüftungsschlitze)
- Mindestabmessungen für Bauteilgrößen bis zu einer Materialdicke von 8 mm = 15 x 15 mm, für Materialdicken ab 8 mm = 20 x 20 mm
- Mindestfläche für Bauteilgrößen bis zu einer Materialdicke von 8 mm = 450 mm², für Materialdicken ab 8 mm = 800 mm²
Beachten Sie: Selbst wenn diese Mindestmaße eingehalten werden, kann die Wärmezufuhr zu Verformungen der Bauteile führen. Solche Verformungen können auch durch im Material vorhandene Spannungen verstärkt werden.
11. Konstruktion des Kernlochs bei Laserteilen
Für die präzise Herstellung von Gewinden ist es entscheidend, das Kernloch in der korrekten Größe vorab zu bohren. Die spezifischen Kernlochdurchmesser variieren je nach der Größe des Gewindes und müssen in der Entwurfsphase beachtet werden. Die zugehörigen Maße finden Sie in der unten aufgeführten Tabelle.
Gewinde | Steigung | Kernloch ⌀ |
---|---|---|
M3 | ×0,5 | 2,5 |
M4 | ×0,7 | 3,3 |
M5 | ×0,8 | 4,2 |
M6 | ×1 | 5,0 |
M8 | ×1,25 | 6,8 |
M10 | ×1,5 | 8,5 |
M12 | ×1,75 | 10,2 |
12. Eckenverrundung bei Laserteilen
Besonders bei der Anfertigung von Aussparungen für Steckverbindungenmuss folgendes beachtet werden:
Die Laserteile haben einen Mindestradius an den Schnittkanten von 0,3mm. Dieser Wert kann je nach Dicke des Materials auch deutlich größer sein. Falls die Konstruktion Ecken mit einem sehr kleinen Radius erfordert muss zwingend mit dem Lieferanten gesprochen werden.